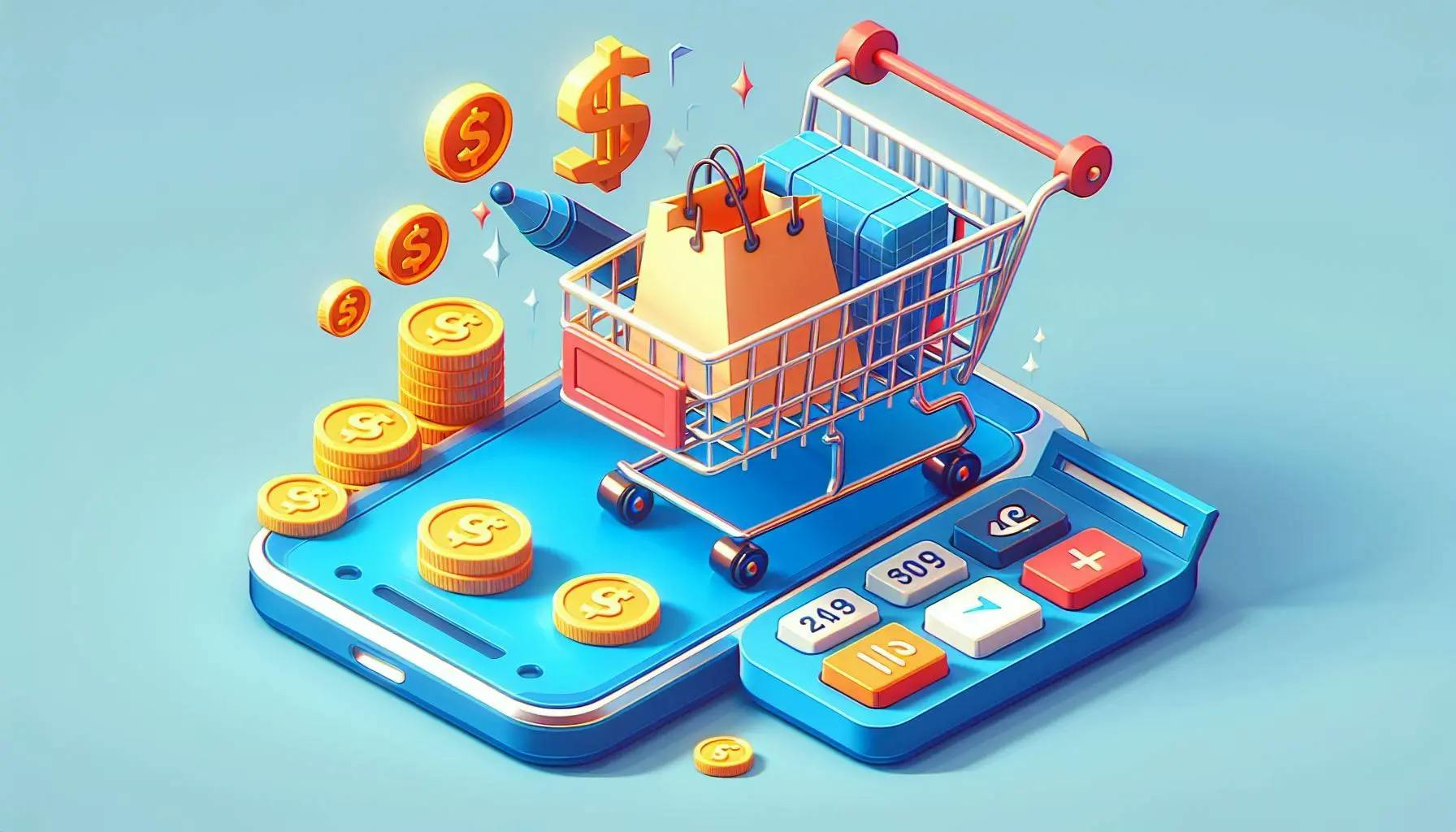
As a construction business owner or manager, you know that cost control is crucial for maintaining healthy profit margins. Just like a skilled chef...
Like a skilled chef carefully measures ingredients to create a delicious dish while minimizing waste, successful construction companies employ various techniques to keep costs in check without compromising quality. In this post, we'll explore seven effective cost control techniques that can help maximize your profitability in the construction industry.
One of the most critical steps in cost control is creating accurate cost estimates before the project begins. This process is similar to creating a budget for a family vacation – you need to consider all the expenses involved to avoid overspending. To develop precise estimates, consider the following:
By investing time in creating detailed and accurate cost estimates, you can set realistic expectations and avoid surprises down the road.
Effective project management is like having a well-organized game plan for a sports team. It ensures that everyone is on the same page, working towards a common goal, and using resources efficiently. To implement effective project management:
With a strong project management system in place, you can minimize delays, reduce waste, and keep costs under control.
Materials often account for a significant portion of construction costs. Optimizing material procurement is like finding the best deals on groceries – you want to get the most value for your money. To optimize material procurement:
By carefully managing your material procurement process, you can ensure that you have the right materials at the right time, while keeping costs in check.
Creating a culture of cost awareness within your organization is like encouraging your family to adopt energy-saving habits at home. When everyone is mindful of costs, small savings can add up to significant amounts over time. To foster a culture of cost awareness:
By involving your entire team in the cost control process, you can tap into a wealth of ideas and create a sense of shared responsibility for the company's financial success.
Embracing technology and automation in construction is like using a dishwasher instead of washing dishes by hand – it saves time, effort, and resources. By leveraging technology and automation, you can:
Investing in the right technology and automation tools can lead to significant cost savings and increased productivity over the long run.
Lean construction is a management approach that focuses on maximizing value while minimizing waste. It's like decluttering your home – you keep what's essential and eliminate what's not. To implement lean construction principles:
By adopting lean construction principles, you can streamline your processes, reduce waste, and improve overall efficiency.
Regular cost reviews and analyses are like periodic check-ups with your doctor – they help you identify potential issues before they become serious problems. To effectively review and analyze costs:
Cost control in construction is an ongoing process that requires a multifaceted approach. By implementing these seven techniques – developing accurate cost estimates, implementing effective project management, optimizing material procurement, fostering a culture of cost awareness, leveraging technology and automation, implementing lean construction principles, and regularly reviewing and analyzing costs – you can create a strong foundation for financial success in your construction business.